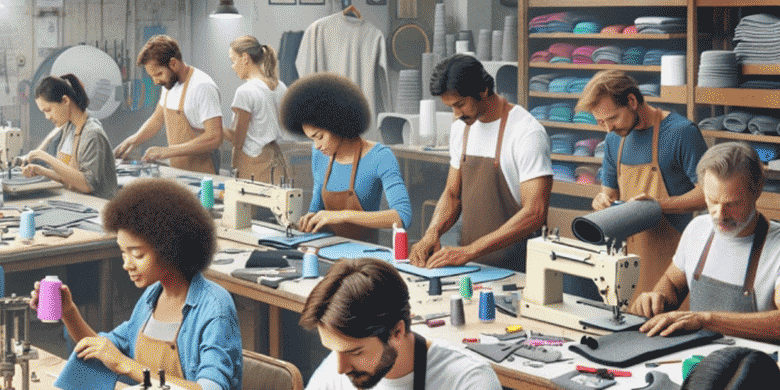
6 September, 2024
How Stubby Holders are Made: A Behind-the-Scenes Look
Stubby holders are more than just a simple tool; they're a craft. Among the various materials used, neoprene stands out as a popular choice due to its excellent insulation properties and durability. Today I am going to explain how they are made covering everything from their construction to the intricate details of stitching, glueing, and printing.
The Making of Neoprene Stubby Holders
Material Selection
The choice of neoprene as the primary material for stubby holders is a deliberate one, driven by its unique properties. It is an excellent insulator, thanks to its closed-cell structure. This property is crucial in maintaining the temperature of beverages, keeping cold drinks cold and preventing condensation on the outside.
Unlike other materials, neoprene combines flexibility with durability. This means it can stretch to accommodate various can or bottle sizes while retaining its shape and strength over time. Its resistance to water, oil, and heat makes it a versatile material, suitable for outdoor events, beach outings, or regular household use. This resistance also means it's easier to clean and maintain.
It is often chosen for its eco-friendliness. Some types are now being made from limestone-based chloroprene rubber, which is less harmful to the environment compared to petroleum-based neoprene. It comes in various densities and thicknesses, allowing manufacturers to choose the right type based on the desired insulation level and the feel they want their custom neoprene stubby holders to have.
Cutting and Shaping
The process of transforming neoprene sheets into stubby holders involves precision and craftsmanship. The die-cutting process uses a custom-shaped die, akin to a cookie cutter, but for neoprene. The sharpness and shape of the die are crucial for ensuring clean cuts and consistent shapes.
The dimensions of the die are tailored to standard can and bottle sizes, but there’s also scope for custom sizes. The goal is to achieve a snug fit that ensures effective insulation and a secure grip. The cutting process also takes into account any design elements that will be added later, such as spaces for seams, printing areas, or additional features like handles or zippers.
Before mass production, prototypes are often made and tested to ensure the fit and functionality are up to standards, especially if the design deviates from the traditional cylindrical shape.
Adding the Extras: Stitching and Glueing
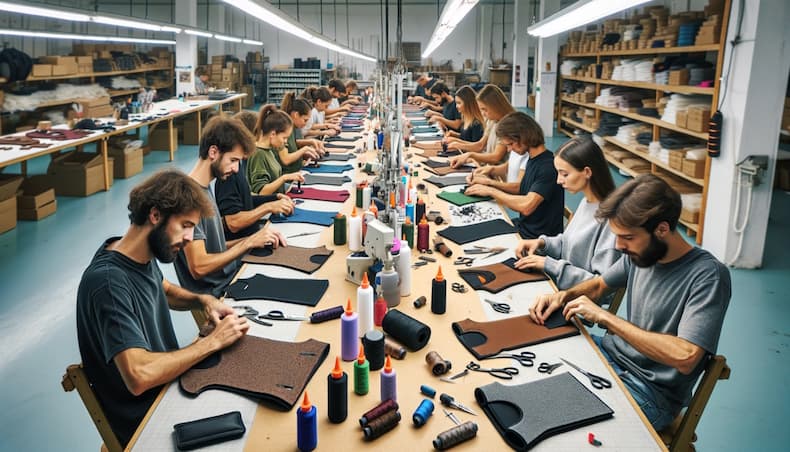
Stitching
The stitching process, is a crucial stage in their production, enhancing both their durability and visual appeal. Firstly, the choice between zigzag and straight stitching is made based on both aesthetic and functional considerations. Zigzag stitching, with its interlocking pattern, is often chosen for its stronger hold and flexibility. Straight stitching, on the other hand, offers a cleaner, more traditional look and can be used where less stretch is required.
The thread used in the stitching is typically of high quality, chosen for its strength and resistance to various elements. It must withstand regular use, exposure to moisture, temperature variations, and frequent washing without fraying or losing its integrity. This is why weather-resistant and durable thread materials are preferred.
The stitching process requires precision to ensure that the neoprene pieces align correctly and the seams are strong and consistent. This precision contributes significantly to the overall appearance and quality of the stubby holder. In some designs, additional reinforcement might be added at the seams to prevent tearing, especially in areas that are likely to experience the most stress when the stubby holder is used.
Post-stitching, there's typically a quality control phase where each stubby holder is inspected for consistency in stitching, alignment of seams, and overall quality. This ensures that each product meets the set standards before it is distributed or sold. The stitching process also allows for customisation. Different colours of thread can be used to complement or contrast with the main colour, and unique stitching patterns can be employed to create distinctive designs, catering to personal preferences or branding requirements.
Glueing
The glueing process is another integral component that contributes to their overall quality and durability. This method is either used as an alternative to stitching or in conjunction with it to enhance the holder's strength.
The choice of glue is crucial. It needs to be strong and waterproof to effectively bond the neoprene pieces. The adhesive must be resilient enough to handle the stresses of regular use, including exposure to different temperatures and moisture, without losing its adhesive properties.
Careful application prevents spillage or excess glue from seeping out of the seams, which could mar the appearance. This requires skilled workmanship and sometimes the use of specialised equipment to apply the glue evenly and accurately.
Once the glue is applied, the neoprene pieces are carefully aligned and pressed together. This may be done manually or with the help of a machine, depending on the scale of production. The pressure applied must be sufficient to create a strong bond but not so much that it causes the glue to spread beyond the seam.
After bonding, the glue needs time to cure. The curing time can vary depending on the type of adhesive used and the environmental conditions. During this time, the glued parts must be kept in a stable position to ensure a strong and even bond as the glue sets. When done correctly, glueing can provide a seamless look that is both aesthetically pleasing and durable. It offers a smooth finish with no visible stitching lines, which can be desirable in certain design aesthetics.
The Art of Printing on Neoprene Stubby Holders
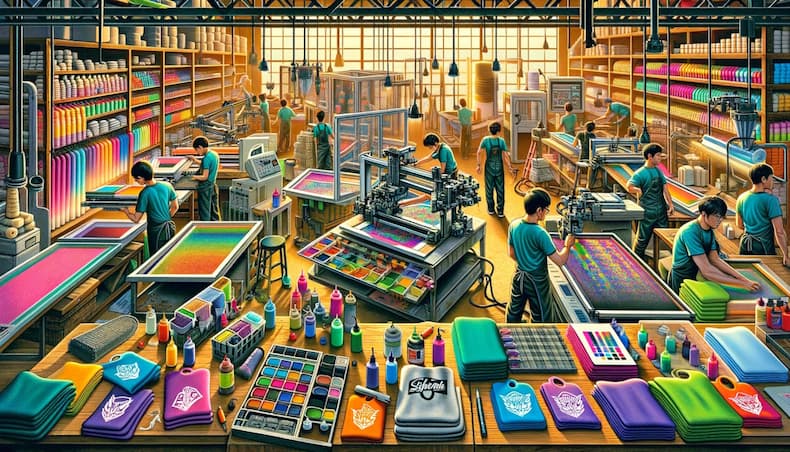
There are several printing techniques available for decorating neoprene stubby holders:
1. Screen Printing
The Process: It involves creating a stencil (or screen), and then using it to apply layers of ink on the printing surface, one colour at a time. Each colour is applied using a different stencil, one at a time, to achieve the final design.
Versatility and Quality: This method is renowned for its versatility and the vibrancy of the colours it produces. It's particularly effective for designs that don't have a lot of colours, as each additional colour requires a separate screen and layer of ink.
Durability: The inks used in screen printing are typically very durable, able to withstand washing and prolonged use without significant fading.
Cost-Effectiveness: For large batches with limited colours, screen printing can be very cost-effective. However, the setup cost for each colour might be high, making it less economical for small batches or designs with many colours.
2. Digital Printing
The Process: Digital printing on neoprene works much like a traditional inkjet printer, but it's adapted to handle the flexible and thick nature of neoprene. It allows for the direct application of ink onto the material without the need for stencils.
Design Flexibility: This method is excellent for complex and multi-coloured designs, including those with gradients and fine details. It offers a full spectrum of colour options without the need for separate screens.
Print Quality: It typically results in a high-resolution and detailed image, but it might not be as durable as screen printing, especially under heavy use or frequent washing.
Cost and Efficiency: While it's more cost-effective for small batches or highly detailed designs, the unit cost for large batches might be higher compared to screen printing.
3. Sublimation Printing
The Process: It involves printing a design onto a special paper, then transferring that design onto the neoprene using heat and pressure. The heat converts the solid dye particles directly into gas, bypassing the liquid stage, and bonds them to the neoprene fibres.
Image Quality and Durability: This technique is known for producing very vibrant, high-resolution images that are embedded into the material rather than sitting on top, resulting in a more durable finish that resists fading and wear.
Design Capabilities: It's excellent for detailed and full-colour images, and is especially effective for photographic and intricate designs.
Material Considerations: Sublimation printing works best on light-coloured or white neoprene, as the dyes are translucent and the colour of the neoprene will affect the appearance of the final print.
Each of these printing methods offers unique benefits, making them suitable for different types of designs and production needs. The choice of technique largely depends on the complexity of the design, the colours involved, the quantity being produced, and the desired durability of the print.
Conclusion
The creation of neoprene stubby holders is a blend of careful material selection, precise crafting, and artistic printing. Whether it's for a backyard barbie, a corporate event, or just personal use, these holders are a testament to skilled craftsmanship and the joy of customisation. Each step in their creation, from the cutting of neoprene to the intricate printing process, contributes to the final product that not only keeps your drink cold but also adds a touch of personality to your beverage experience.
The Stubby Holders Team